
Quality Management Systems
If you find that your Quality Management System (QMS) is hindering your efficiency, it may be time to reassess and streamline your processes. Streamlining your processes can help eliminate inefficiencies, reduce costs, and improve overall productivity. By reassessing and optimizing your Quality Management System (QMS), you can ensure that it supports your business goals rather than hindering them. Being proactive allows you to stay competitive and responsive to identified risks.
The QMS Support service includes four main approaches: Implementation, Assessment, Remediation & Management
QMS Implementation
This approach involves developing and implementing a fit-for-purpose QMS tailored to the organization's needs. It includes establishing the foundational pillars of the QMS, such as the quality policy, quality manual, and other essential components. Training staff on the new processes is part of the implementation and a QMS effectiveness check can also be performed as needed.
Gap Assessment
QMS Gap Assessments are common when organizations are advancing through the clinical stage and want to ensure their QMS remains compliant. In this approach, I will conduct thorough assessments to identify areas that need to be updated to meet more rigorous requirements. A remediation plan with actionable recommendations will address any identified gaps.
QMS Remediation
This service focuses on implementing corrective actions to address deficiencies identified from the gap assessment. I will update SOPs, enhance training programs, deliver training sessions, and make necessary adjustments to strengthen your quality management processes. Additionally, I will conduct effectiveness checks to ensure that the implemented changes are working as intended and that your QMS is robust, effective, and fully compliant.
QMS Management
This service focuses on the ongoing management and maintenance of your QMS. It includes continuous monitoring, regular updates to SOPs, and metrics monitoring to ensure your QMS remains robust, effective, and compliant. Given the longer-term nature of this assignment, the Head of QA Fractional Consulting service may be more appropriate. Let's connect to discuss the details and find the best solution.
The Simple Approach to QMS Implementation

The "Simple" way of doing things isn't about cutting corners. It's about thorough planning and regular communication with the client to ensure we're always on the fast track. My approach is grounded in Project Management principles to ensure tasks stay within agreed timelines and budget, and we can proactively identify potential delays or roadblocks.
This approach is applied not only to QMS Support services (QMS Implementation, Gap Assessment, Management, or Remediation), but also to any other complex service rendered. This structure ensures that every aspect of the project is managed efficiently and effectively.
Initiation
Planning
Execution
Monitoring
Closing
Define project goals, objectives, scope. Identify key stakeholders, obtain necessary approvals to proceed.
Develop project plan with timelines and a Project Charter outlining project's purpose and deliverables.
Agree on implementation method, identify team if applicable. Manage and execute tasks as planned. Regular communication to keep stakeholders informed.
Monitor project performance, track key metrics, identify deviations, and implement corrective actions to keep the project on track.
Complete project tasks, finalize documentation, and obtain acceptance of deliverables.
Gap Assessment: How robust is your QMS?
Is your QMS...
IN PLACE?
IN USE?
IN CONTROL?
SUSTAINABLE?
It is crucial to regularly assess the efficacy and suitability of your existing Quality Management System (QMS) through periodic reviews of processes.
This can be achieved by establishing metrics, Key Performance Indicators (KPIs), and other process controls. These measures help identify risks and trends, enabling proactive actions to maintain and improve the QMS.
The QMS Gap Assessment Process
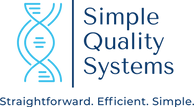
The QMS gap assessment will identify areas where your current quality management system falls short of industry standards and regulatory requirements. By pinpointing these gaps, we can prioritize actions to enhance compliance and improve overall quality. Following the assessment, we offer QMS remediation services to address identified gaps and ensure your system meets all necessary standards.
Through the QMS initial assessment we will identify main pain points as well as areas of opportunity to make your existing processes more efficient and compliant. This proactive approach not only enhances compliance but also fosters a culture of continuous improvement leading to increased stakeholder confidence.
Gap-Assessment Workflow
Prepare
How we'll do it: Gather relevant documentation, survey SMEs to identify current process pain points.
Timeframe: Typically takes 1-3 weeks, depending on complexity and availability of documentation and staff.
Plan
How we'll do it: Prioritize gaps based on impact. Assign responsibilities, set deadlines, and allocate resources. Create a timeline for changes.
Timeframe: 1-2 weeks, depending on the number of gaps and complexity.
Evaluate
How we'll do it: Conduct follow-up audits, gather feedback, and review performance metrics. Adjust as needed to maintain compliance and improvement.
Timeframe: 2-4 weeks, depending on complexity and data availability.
Assess
How we'll do it: Conduct interviews, review documents, and perform assessment to gather data. Checklists and assessment tools will be produced.
Timeframe: 2-4 weeks, depending on organization size and assessment thoroughness.
Implement
How we'll do it: Implement changes, update documentation, and train employees. Monitor progress and adjust as needed.
Timeframe: 4-12 weeks, depending on changes and resources.
DID U KNOW?

Contrary to popular belief, paper-based systems are acceptable, especially in the early development stages. The key is to ensure these processes are well-controlled and compliant until you are able to invest in the implementation of an electronic QMS.
Result?
A Fit-for-purpose QMS
Explore QMS Remediation Services
QMS Remediation
QMS Remediation is essential after a gap assessment. First, identify the gaps, then remediate them. Remediation activities can be applied to a single process or the entire QMS program, depending on your needs. Upon request, a QMS effectiveness check can be performed at the end of the remediation project.
Identify the Gaps/Fix the Gaps
Gap Assessment
-
Team Collaboration
-
Interview staff
-
Identify Pain Points
-
Gather surveys
-
Document Review (SOPs, forms, etc)
-
Write Gap Report
-
Provide list of recommendations
Remediation
-
Gaps identified and remediation plan generated
-
Update procedures and related documents
-
Provide training to staff
-
Effectiveness checks
-
Conduct internal audit, if needed.
Quality Projects

QMS Support Services also encompass the management and execution of a wide variety of single quality initiatives or projects. For example, I can assist with the implementation of a new electronic eQMS, conduct workshops on technical writing or other quality topics, or create quality dashboards on Power BI, to name a few. Whatever your requirements, we can collaborate to develop a tailored plan that meets your needs.
Additionally, we offer targeted gap assessments of individual key quality processes rather than evaluating the entire program. Some examples of processes that can be individually assessed include:
Training Program
Change Management
Deviations/CAPAs
Audit Program
Vendor Mgt & Oversight
Risk Management

QMS Building Blocks
Is your quality organization built on a solid foundation? Without a structured QMS, there may be inefficiencies in processes, leading to increased costs and delays in product development. Simple Quality Systems can also assist you by developing these blocks.
Free Consultation
30 min
Free
Other Related Services Offered
Explore all other service offerings. Schedule a free 30-minute video consultation or request a quote for additional information.
- Available Online
Fractional Consulting: High-level QA expertise at a fraction of the cost